06 Giu 2018
Un materiale dalle mille vite
Grazie a Rilegno e alle aziende di riciclo il legno diventa risorsa dalle vite infinite
Quando si dice che il legno è il materiale dalle mille vite non si esagera. Il suo ciclo può infatti durare all’infinito, con benefici ecologici ed economici. Riciclare il legno significa risparmiare energia, migliorare lo stato qualitativo dell’aria e al contempo evitare gli sprechi. Per questo è fondamentale che a fine uso non finisca in discarica: meglio raccoglierlo, recuperarlo e farlo rinascere a nuova vita. A farlo ci pensa Rilegno, che così trasforma il rifiuto in risorsa. E non mancano le aziende che si sono specializzate nell’utilizzo del legno di recupero nel loro business.
Gruppo Saviola
“Stiamo recuperando legno, aiutateci a salvare gli alberi”. Recita così la frase riportata sulle centinaia di camion del Gruppo Saviola (1.380 dipendenti, 552 milioni di fatturato e un milione di tonnellate di legno riciclato ogni anno) che ogni giorno percorrono la penisola. Se c’è una realtà che ha contribuito in modo determinante alla diffusione della raccolta e del riciclo del legno nel nostro Paese, questa è senza dubbio l’impresa viadanese, colosso del pannello ecologico. Quando Rilegno vide la luce, venti anni fa, poté contare su un grande alleato per sviluppare il suo sistema di raccolta e avvio al riciclo di legno post consumo: Mauro Saviola, il primo riciclatore italiano che credette nelle potenzialità del Consorzio, garantendogli fin dai primi momenti una collaborazione e un appoggio che si riveleranno fondamentali per renderlo ciò che è oggi. Figlio di un ebanista, apprendista già all’età di undici anni, dagli anni Sessanta Mauro Saviola inizia a produrre pannelli utilizzando la parte meno pregiata dei pioppi. Dai primi anni Ottanta inizia a recuperare gli scarti da lavorazione industriale (segatura) e poi negli anni Novanta anche il legno post consumo e gli scarti domestici. Grazie all’innovazione tecnologica il Gruppo (oggi guidato dal figlio maggiore del fondatore, Alessandro) passa dalla produzione di pannelli grezzi al pannello nobilitato e infine, nel 1997, al pannello ecologico realizzato al 100 per cento con legno da riciclo.
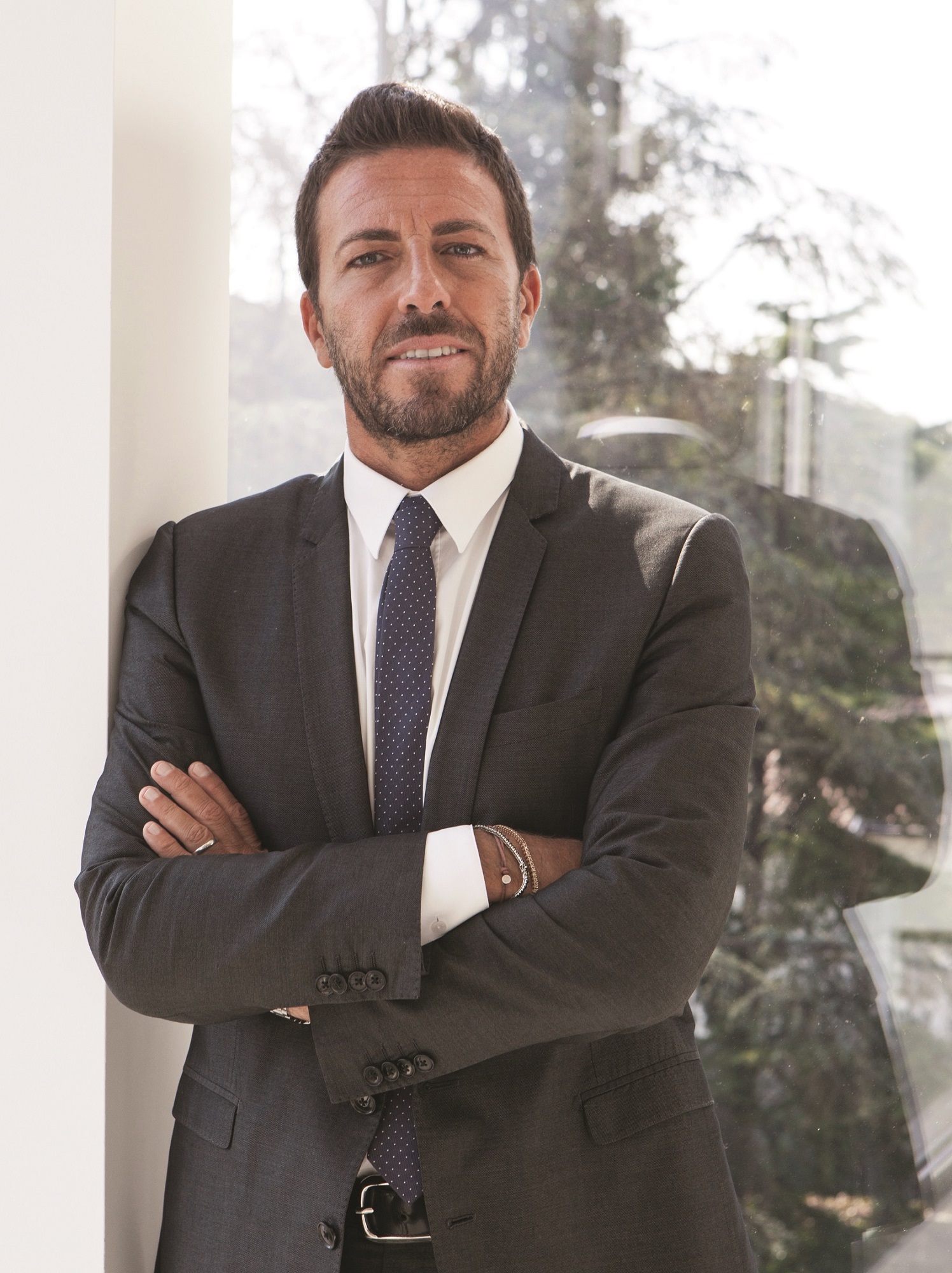
Alessandro Saviola, Gruppo Saviola
Fantoni Spa
Paolo Fantoni è amministratore delegato di Fantoni Spa, multinazionale italiana leader nella produzione di pannelli in Mdf e truciolare, di laminati e carte melamminiche e protagonista nel panorama dei mobili per ufficio e dei sistemi fonoassorbenti. Fondata nel 1882, l’azienda è da sempre guidata dalla famiglia Fantoni (ormai alla quinta generazione) e ha sede principale a Osoppo, in provincia di Udine, dove lavorano oggi 700 dipendenti in un’area complessiva di circa 1 kmq. Il Gruppo Fantoni è cresciuto nel tempo e ha oggi sedi e aziende in Italia e in Europa. Fantoni punta sull’attenzione alla qualità, al benessere e all’ambiente, peculiarità sistematicamente attestate con continue certificazioni dei processi, dei materiali e dei prodotti finiti. “La sostenibilità deve essere un impegno comune a tutto il settore del legno e dell’arredo”, spiega Paolo Fantoni. “Non sono solo le norme a spingerci in questa direzione, ma anche un imperativo etico. È necessario farci carico di tutto il ciclo che dalla produzione arriva fino alla vendita finale dei prodotti”, è l’invito del numero uno dell’azienda. Ricorda che dal 2021 i produttori europei di materassi avranno la responsabilità del ritiro e riciclo dei prodotti. “Questo concetto di economia circolare deve permeare tutto il comparto”, conclude Fantoni.
Paolo Fantoni, Fantoni Spa
Gruppo Frati
Il Gruppo Frati, 300 milioni di fatturato, 800 dipendenti e una capacità produttiva di oltre 4.000 metri cubi al giorno, è sul mercato dal 1961 ed è tra le aziende leader in Europa produttrici di pannelli truciolari. “Il 100% del legno che utilizziamo è post-consumo e certificato FSC”, racconta Alfio Sarzi Amadé, dirigente dell’Ufficio acquisti della società, che negli anni ha ottenuto altre numerose certificazioni sul tema della sostenibilità. “Questo materiale proviene da tutta Italia, e viene raccolto sia presso Ecostazioni pubbliche (Raccolta differenziata dei Comuni) che presso centri di stoccaggio privati. Alla raccolta provvediamo in gran parte con nostra struttura e nostra organizzazione, reimmettendo in circolo materiale giunto a fine uso ed evitando così lo smaltimento tramite discarica o combustione con conseguente emissioni in atmosfera di CO2”.
Alfio Sarzi Amadé, Gruppo Frati
Saib
Saib nasce a Caorso (PC) nel 1962 dall’idea di riutilizzare gli scarti di altre lavorazioni del legno per creare pannelli truciolari. Con un fatturato di 105 milioni nel 2016, Saib ha due linee di produzione in continuo per il pannello grezzo e quattro impianti di nobilitazione. Da oltre vent’anni utilizza per la propria produzione solo rifiuti di legno post consumo. Ogni giorno oltre 100 camion di rifiuti di legno vengono trasformati attraverso un complesso processo di produzione in pannelli truciolari destinati all’industria dell’arredamento. “Quando sono entrato in azienda vent’anni fa”, racconta l’amministratore delegato di Saib Giuseppe Conti, “già utilizzavamo il legno di recupero, ma il mercato di vendita non era ancora pronto per capirne l’importanza. Oggi, invece, è finalmente diventato un plus offrire al mercato un prodotto riciclato. Sono cambiati i consumatori ed è il cliente finale a chiedere prodotti che rispettino veramente l’ambiente. Noi siamo una concreta dimostrazione di come l’economia circolare possa rappresentare anche un’opportunità di crescita per le aziende.”
Xilopan
Fa parte della filiera Rilegno anche Xilopan, azienda di Cigognola (PV), nel cuore della Pianura Padana, zona ad elevata concentrazione di pioppeti, dove seleziona legni vergini provenienti dalle colture locali e certificate per produrre pannelli in truciolare 100% pioppo italiano.
L’utilizzo del legno riciclato non si esaurisce con la produzione dei pannelli
Sicem Saga
L’utilizzo del legno riciclato non si esaurisce con la produzione dei pannelli. Il gruppo Sicem Saga (nato nel 1960) è l’unico produttore italiano di pasta per carta destinata al mercato, principalmente italiano ma con quote di export (40% circa) in continua crescita, non solo in Europa ma anche in Medio Oriente, Cina e Far East. La materia prima utilizzata è legno di recupero proveniente dall’industria dei compensati e pioppo da piantagione, ma già da una decina di anni la ricerca e parte degli investimenti sono stati rivolti a sviluppare una tecnologia idonea all’utilizzo di legno post consumer proveniente da imballaggi, che una volta selezionato ed eliminate le impurità viene utilizzato in diverse tipologie di carta anche di qualità. Nei prossimi anni il piano ambientale dell’azienda prevede investimenti cospicui per ridurre la quantità di risorse utilizzate e aumentare la percentuale di legno post consumer.
Isotex
Isotex da oltre trent’anni produce blocchi cassero e solai in legno cemento ed è oggi la maggiore realtà europea nel settore. “Il legno è da millenni la materia prima più utilizzata”, dicono Loris ed Eros Chinello, titolari dell’azienda. “In virtù delle buone prestazioni termiche del conglomerato legno-cemento e delle possibilità di riutilizzo di materie prime pregiate, questo sistema viene impiegato anche da chi è sensibile alle tematiche ambientali e da chi costruisce secondo i canoni della bioedilizia”. Nell’esperienza di Isotex, il legno di recupero, proveniente dalla raccolta, deve essere abete perché è la tipologia con la maggiore conducibilità termica e la migliore compatibilità con il cemento. Il legno avviato a questa tipologia di recupero è attentamente controllato, ripulito da eventuali impurità e ridotto di volume. Il cippato di legno viene poi miscelato ad una soluzione di minerale naturale con acqua e con cemento e l’impasto che si ottiene viene modellato in stampi di varie misure per formare i blocchi cassero Isotex. Il legno conferisce leggerezza ai blocchi e la superficie macroporosa conferita dal conglomerato legno-cemento favorisce la traspirazione delle pareti e un buon supporto per gli intonaci di finitura.
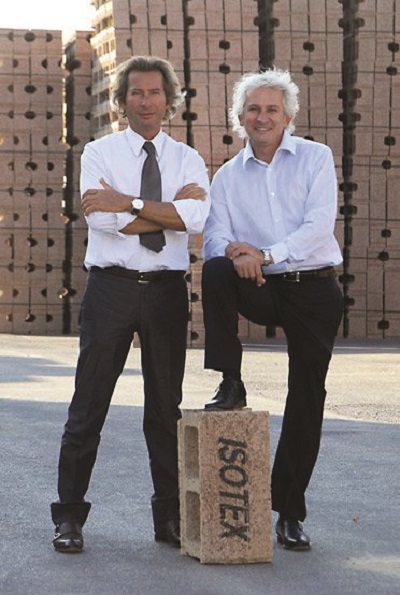
Loris ed Eros Chinello, Isotex
Nel settore non operano solo aziende storiche. Ecobloks è nata nel 2014 per fornire ai produttori di pallet un blocchetto in legno truciolare pressato, a differenza del concorrente estero, composto dal 100% di legno riciclato. Ecobloks nel 2017 ritirerà circa 100.000 tonnellate di rifiuti legnosi che, dopo essere stati macinati, vagliati e lavorati, diventeranno 130.000 metri cubi di blocchetti per pallet. I clienti si concentrano per il 60% in Italia (terzo produttore di pallet in Europa, con più di 400 aziende produttrici); a seguire Francia, Germania, la maggior parte dei paesi Ue e alcuni paesi extra Ue (Turchia, Marocco).
Massimiliano Spallanzani, Ecobloks
Rilegno20 – la rivista
Questo articolo è estratto dalla nostra rivista Rilegno 20, realizzata per celebrare i vent’anni del consorzio. Clicca sull’icona sottostante per leggerne il pdf!